What is the National Aerosol Facility?
The nuclear reactors run by the Department of Atomic Energy satisfy two critical needs of our nation – nuclear energy and strategic usage. The reactor safety is analyzed by doing a scenario assessment because one cannot simulate the experimental settings in a laboratory. Regardless, we must know about the mishaps and potential damage. The idea of a nuclear energy program is to have all safety nets in place, and how to assess it is by running the safety course. The problem faced is that they can create their code to determine the safety of their reactors, but that requires validation of the code using experimental settings. The National Aerosol Facility was set up to analyze the safety of the reactors.
About the facility
After joining IIT Kanpur in 2003, Professor S. N. Tripathi, who had previously worked at BARC, launched the National Aerosol Facility. The facility was supposed to be built in 2018–19, but the pandemic caused the construction to be put off by more than two years. Most components and equipment are designed by BARC scientists and experts at IIT Kanpur and are indigenously made. There are around 7-8 such facilities globally, with this being the first in South Asia. Since its inception, four experiments have been conducted, collaborating with over ten scientists.
Why did we choose IITK to be the center?
Post independence, advancement in industrialization led to a desperate need for energy, and Nuclear Energy was viable. Since India didn’t sign the Nuclear Nonproliferation Treaty, other nuclear countries were not ready to provide technologies to India. In 1998, after the nuclear test in India, the situation worsened due to sanctions imposed by the USA. There was a way – to transfer knowledge in this field via educational institutes, and IIT Kanpur was one such institute.
How does the facility function?
The facility encompasses two groups, one works on reactor safety (Reactor Safety Division) and the other on radiation protection (Radiological Physics & Advisory Division). There’s an Address Resolution Protocol (ARP) to review the safety parameters.
Half of the funding for the facility comes from the institute, and the other half comes from BARC and BRNS in equal amounts. The total funding sums up to about 20 crores.
What problem statement is the NAF working on?
When an accident occurs in a nuclear power plant, radioactive material is released into the environment and deposited inside the power plant, which may escape into the environment. This material can be in the form of aerosols. The NAF experiments study the behavior (size, growth, properties, etc.) of such radioactive aerosols and the amount of aerosol being deposited and resuspended. The goal is also to create a database from the experiments done here and use these databases to validate the accidental nuclear codes
How does the NAF work?
Two plasma torches in the facility are used to generate plasma. Argon is used as it isn’t expensive like helium or flammable like hydrogen. It is mixed with nitrogen to increase its enthalpy.
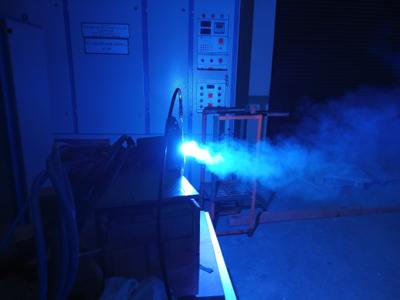
Argon or nitrogen is also used as the carrier gas to ensure that the plasma flame doesn’t extinguish. The powder feeder directly feeds Zinc and Tin powder to the plasma flame. Upon reaching the flame, the metal powder vaporizes and goes on ahead to condense into small particles. More vapor gets deposited on the smaller particles to become bigger particles. The particle size increases as more vapor gets deposited on the smaller particles, or the particles coagulate.
And thus, aerosols are generated from Zinc or Tin metal powder. As the metal vaporizes, the aerosols react with oxygen and forms zinc oxide or tin oxide.
Air for a compressor can be used along with Helium or Argon as a carrier gas. The mixing vessel ensures that the generated aerosol gets the proper time and space to reach the required concentration and ensures a stabilized flow of the aerosols. The two plasma torches are beneficial as they make it possible to generate a very high concentration of aerosols or to check for a mixture of two different aerosols.
The centerline temperature of the plasma flame is almost 10000C. Water circulation reduces this temperature, ensuring the flame-generating electrodes do not melt.
A high voltage is supplied to the gas, creating a vast electric potential, thereby ionizing the gas, and generating plasma. Initially, the frequency is kept high and alternating to create a spark that produces plasma. It is later shifted to DC, and the plasma keeps generating.
There are two different pipe sections for the supply of different gases. Pressure and flow control valves are present for each pipe to control the pressure and flow of the gases.
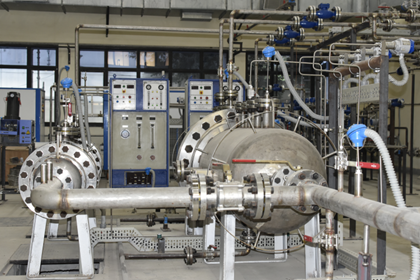
The design pressure for the facility is 10 bar, and some components can sustain forces up to 16 bar. However, still, it is preferred to stay within the operating pressure of 5 bar. A thermal mass flow meter and vortex flow meter are used to measure the mass flow rates of the gases and steams.
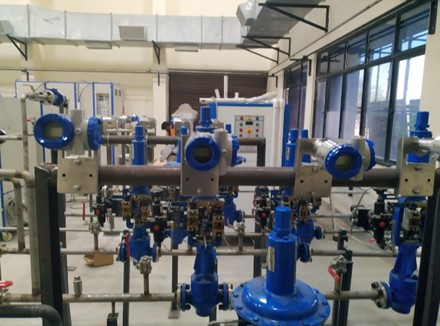
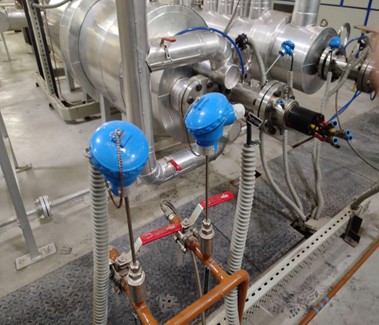
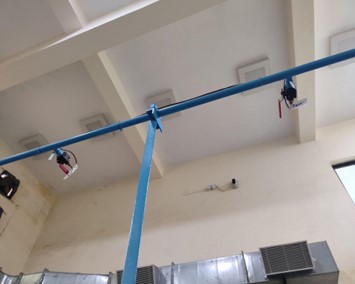
The facility has a boiler to observe the interaction of the aerosol particles with steam since steam is also present in the environment with other gases whenever an accident occurs in a nuclear power plant. Due to its interaction with aerosol, the steam condenses to water, which can be problematic as it can create hydrogen and leads to explosions.
Two heaters (air pre-heater and air superheater) are installed to mimic the high-temperature scenarios in which accidents occur. After passing through these heaters, the components are mixed in the mixing vessel, and then they go ahead. That panel is the heat control panel.
The central core contains nuclear fuels; during accidents, melting occurs (called corium), and the temperature crosses 2000C.
Mineral wool is used for insulation to avoid heat loss. This mineral wool is protected by using an aluminum sheet over it.
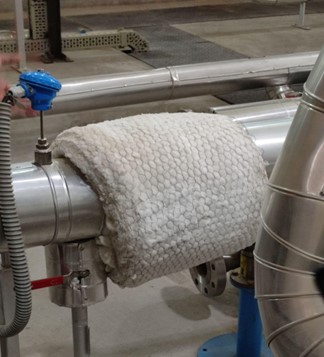
After evaluating the critical parameters, the aerosol-laden gases enter the scrubber tank filtration unit. The aerosols are filtered in this unit, and the clean gases, without any particles, move ahead. The scrubber tank has an inbuilt mechanism to maintain its water level automatically. The pressure is maintained inside the scrubber tank using Pressure Vacuum Relief Valve. The clean gases then go to the collection chamber to remove the moisture, which is vented through the vent pipe.
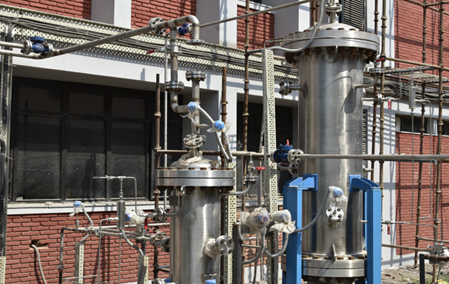
The piping system can be cleaned using high-pressure water through the water inlet port. The water and impurities are then allowed into the drain through the drainage system.
The PDPA instrument uses four laser beams to measure the aerosol particle velocity, size, and concentration via the backscattering technique.
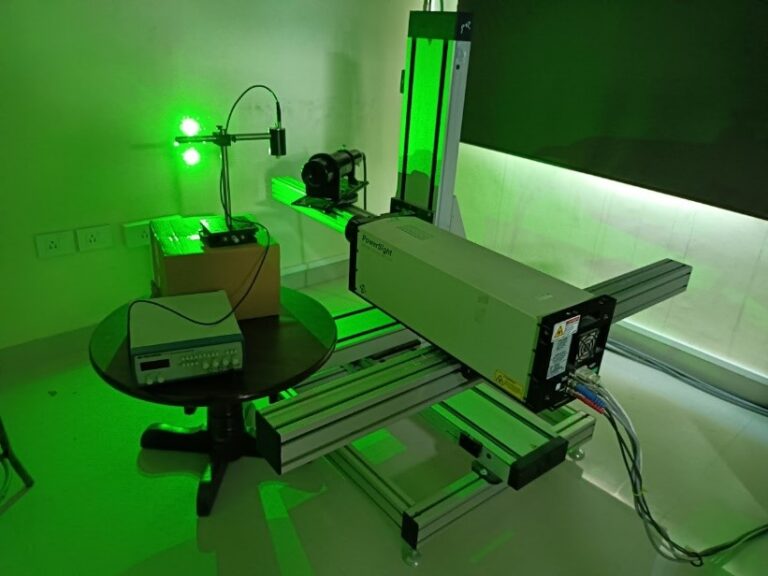
The upper floor of the NAF is dedicated to the control room. The control room hosts the PLC through which the whole NAF working can be monitored and controlled.
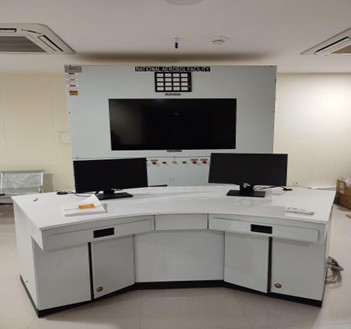
The road ahead?
So far, things have been going smoothly. The facility is self-sufficient concerning human capital and has assisted in publishing about a dozen research papers. The facility is expected to initiate more such projects in the future. It is also planned to set up a safety committee for the NAF.
An international workshop is scheduled that the DAE chairman will inaugurate. The workshop will witness participation from countries like Spain, Japan, South Korea, etc., with good collaborations with the facility.
Written by: Aashi Shrivastava, Aviral Upadhyay, Shreyash Kumar
Edited by: Mohika Agarwal, Sanika Gumaste
Design by: Sachidanand Navik, Shivam Rathore